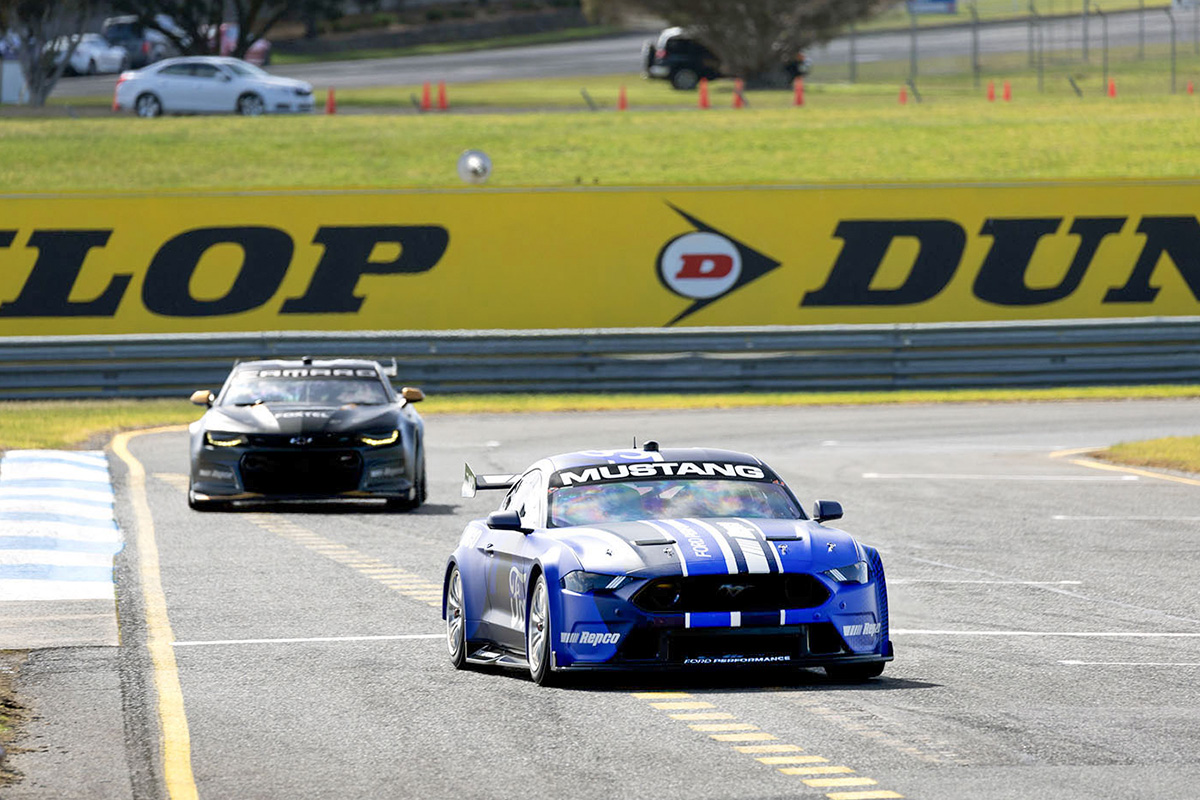
Supercars’ Head of Motorsport Adrian Burgess has moved to ease concerns surrounding the supply of parts for Gen3 chassis.
Earlier this week, Erebus Motorsport CEO Barry Ryan voiced “major concern” over the issue, as reported by Speedcafe.com.
Gen3 will debut in next year’s Repco Supercars Championship, which is slated to kick off at Newcastle from March 10-12.
Despite the project’s development being drawn out, there have been encouraging signs of late, with Triple Eight reporting good progress and Brad Jones Racing taking delivery of its first chassis from PACE Innovations last month.
Thus far, chassis builders have only been able to work on the rear clip and centre section, though the front clip has now been signed off.
It means the build of complete chassis will now be able to flow.
Erebus is constructing its chassis from kits supplied by PACE, having completed as much as it can of its first shell, which will be skinned as a Chevrolet Camaro, prior to the front clip being approved.
However, Ryan’s concern revolves around the “200 or so parts that aren’t released yet”.
Some of the parts that still need to be finalised include the roll bar adjusting system, driver leg protection, and other cabin items.
It is a lengthy process to finalising components given the nature of Supercars’ first-ever control chassis.
Following the design process, parts have been run on the Camaro/Mustang prototypes as a means of a durability test.
The release process then sees hundreds of drawings collated before being sent to the relevant parts tender supplier, or teams to manufacture in-house or utilise an external manufacturer.
In the example of the front clip, previously Supercars teams designed and produced parts themselves to fit to the car.
Gen3 sees a focus on control components, taking the independent design process out of the equation.
To help ease the pressure, Burgess revealed Supercars has issued teams with pre-release drawings for some components to get a head start on manufacturing.
As such, teams have an idea of what to expect and should not be caught off-guard when the final drawings are signed off on.
Burgess explained the project is now moving into its mass-production phase.
“It’s completely different if you’re doing the old school way and the teams are just making their own suspension for their own cars,” Burgess told Speedcafe.com, referring previous generations of Supercars.
“[The teams] miss out a lot of that process because they’re only making two sets for their own cars.
“But when you’re building something that you want every team and every car to have exactly the same component, the process is a little bit more long-winded to make sure everybody has got the right information.
“That’s the difference between mass production and prototyping.
“At the moment our two cars are prototypes and the short-winded process was very much what happened.
“But now we’ve got to turn this into a mass-produced car, then you have to put the time and energy into the detail, otherwise you have people making the wrong part.
“All that’s going to do is waste time and money.
“So you’re better off putting the time and energy into the detail to make sure the finished product is right.”